Mining is one of the most demanding industries in the world, requiring robust and reliable equipment to extract minerals from the earth. Among the various tools used in mining, rockbreaker attachments stand out for their ability to enhance both efficiency and safety. In this blog post, we will explore how these powerful attachments have become indispensable in mining operations, their benefits, and best practices for their use.
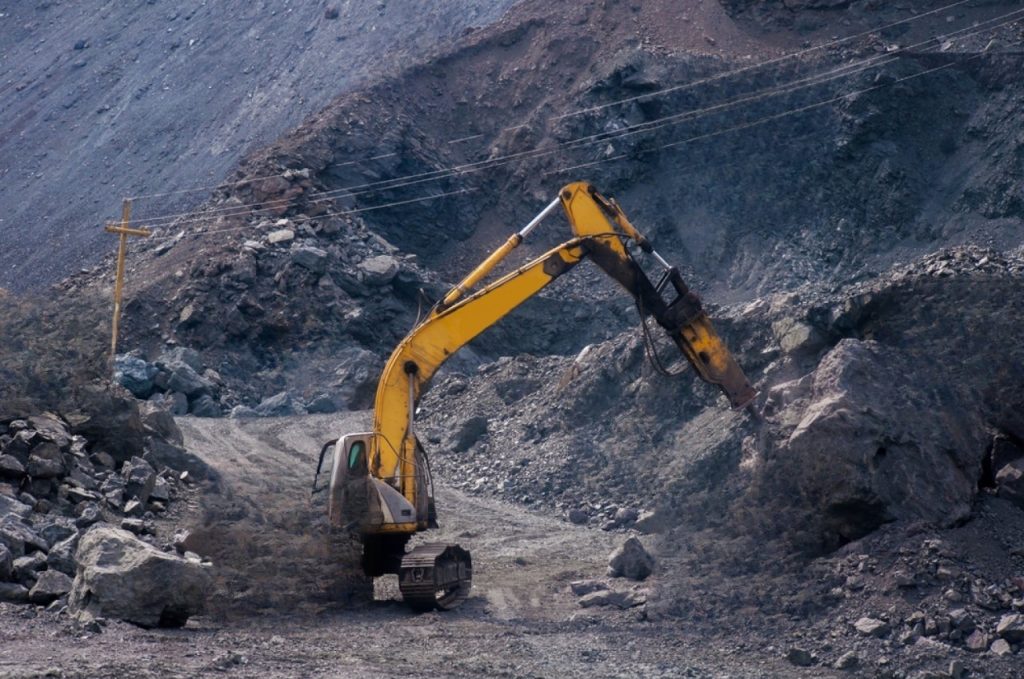
The Role of Rockbreaker Attachments in Mining
Rockbreaker attachments are hydraulic tools mounted on excavators, backhoes, or stationary booms to break rocks and boulders into smaller, more manageable pieces. They are essential in mining operations for several reasons:
- Primary Breaking: Rockbreakers are used to break oversized rocks that are too large to pass through the crushers. This is often the first step in mineral processing.
- Secondary Breaking: After initial blasting, rockbreakers can further reduce the size of rock fragments, making them easier to handle and process.
- Clearing Blockages: They are also employed to clear blockages in crushers and other equipment, ensuring continuous operation and reducing downtime.
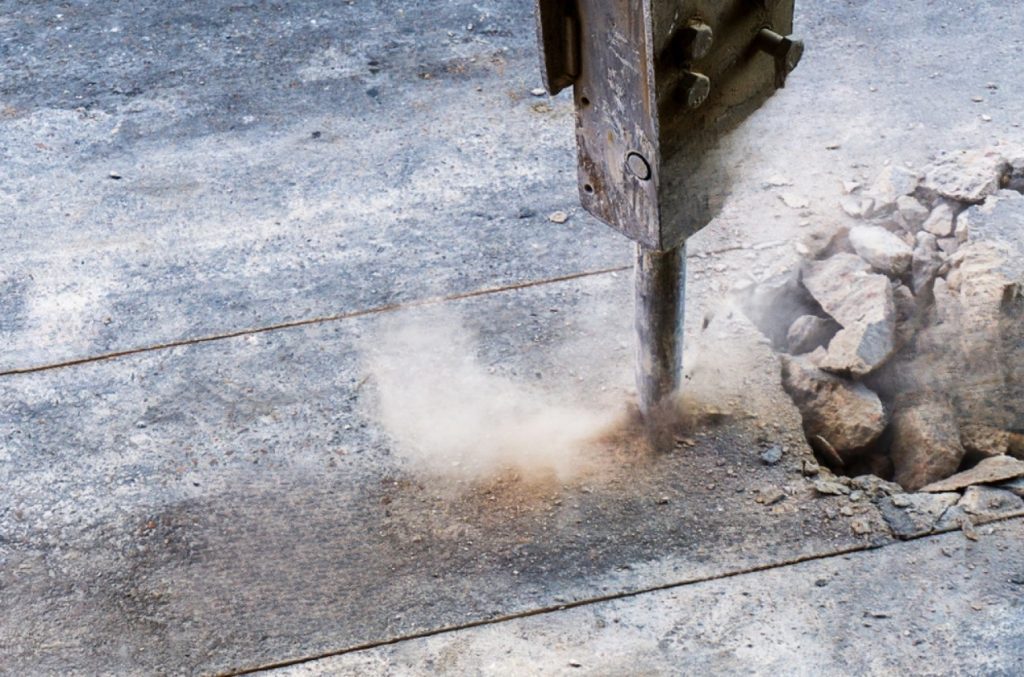
Enhancing Efficiency
Increased Productivity
Rockbreaker attachments significantly increase productivity by reducing the time required to break down large rocks. Unlike traditional methods, such as manual labor or less specialized equipment, rockbreakers provide precise and powerful blows that expedite the breaking process. This leads to faster processing times and increased throughput.
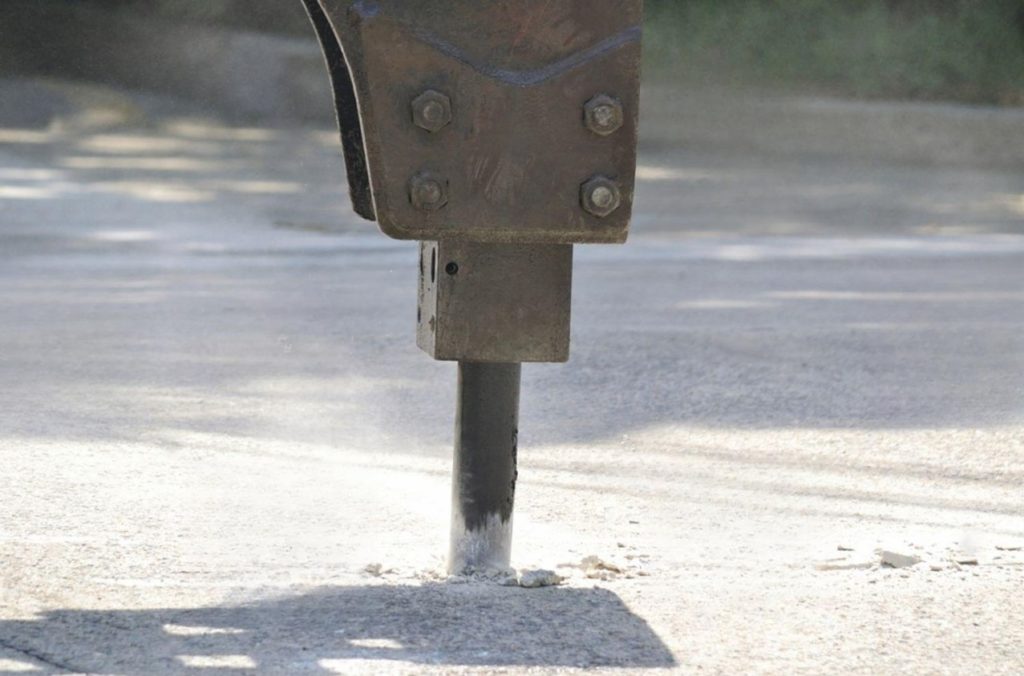
Versatility
Modern rockbreaker attachments come with various chisel options and can be adjusted to suit different rock types and mining conditions. This versatility ensures that mining operations can quickly adapt to different challenges without needing to switch equipment, thus maintaining efficiency.
Automation and Remote Control
Advancements in technology have led to the development of automated and remotely controlled rockbreaker systems. These systems allow operators to control the equipment from a safe distance, reducing the risk of injury while maintaining high efficiency. Automation also ensures consistent performance, reducing human error and fatigue.
Enhancing Safety
Reducing Manual Labor
One of the primary safety benefits of rockbreaker attachments is the reduction of manual labor. By mechanizing the rock-breaking process, workers are less exposed to the physical dangers associated with manual breaking, such as flying debris, repetitive strain injuries, and accidents.
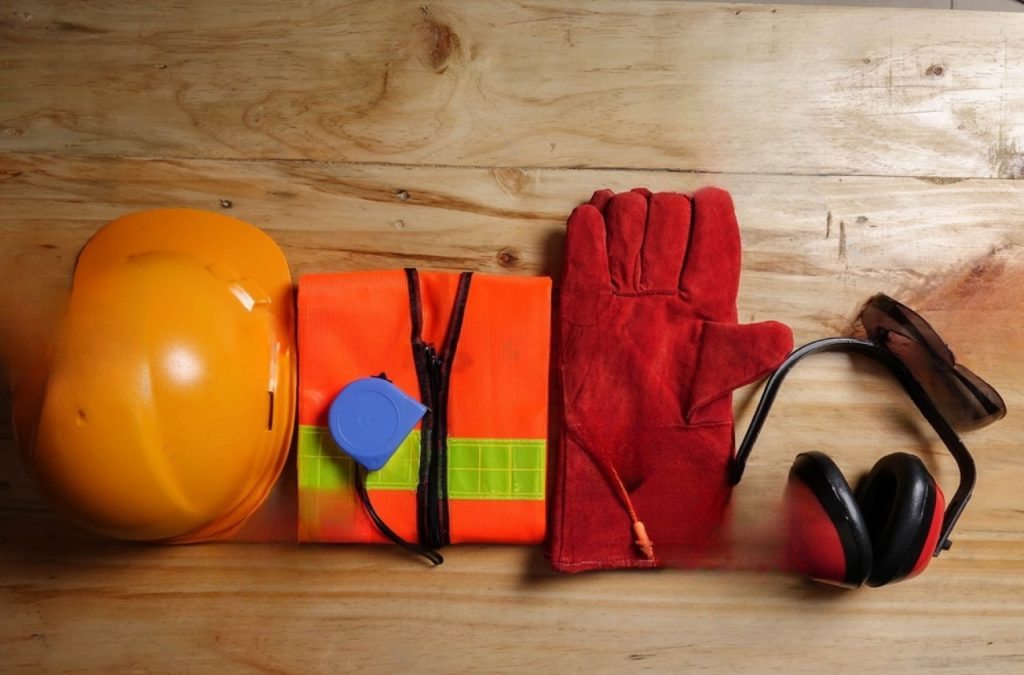
Improved Site Safety
Rockbreakers improve overall site safety by eliminating the need for blasting in certain scenarios. Blasting is a hazardous process that can lead to accidents and requires extensive safety measures. By using rockbreakers for primary and secondary breaking, mining operations can minimize the need for explosives, reducing the associated risks.
Remote Operation
As mentioned earlier, remote control and automation are significant safety enhancements. Operators can control rockbreakers from safe locations, away from the immediate hazards of the mining site. This reduces the risk of injury from falling rocks, equipment malfunctions, and other site-specific dangers.
Best Practices for Using Rockbreaker Attachments in Mining
Proper Training
To maximize the benefits of rockbreaker attachments, operators must be adequately trained. Training should cover equipment operation, maintenance procedures, and safety protocols. Well-trained operators are more efficient and can respond quickly to any issues that arise, ensuring smooth operations.
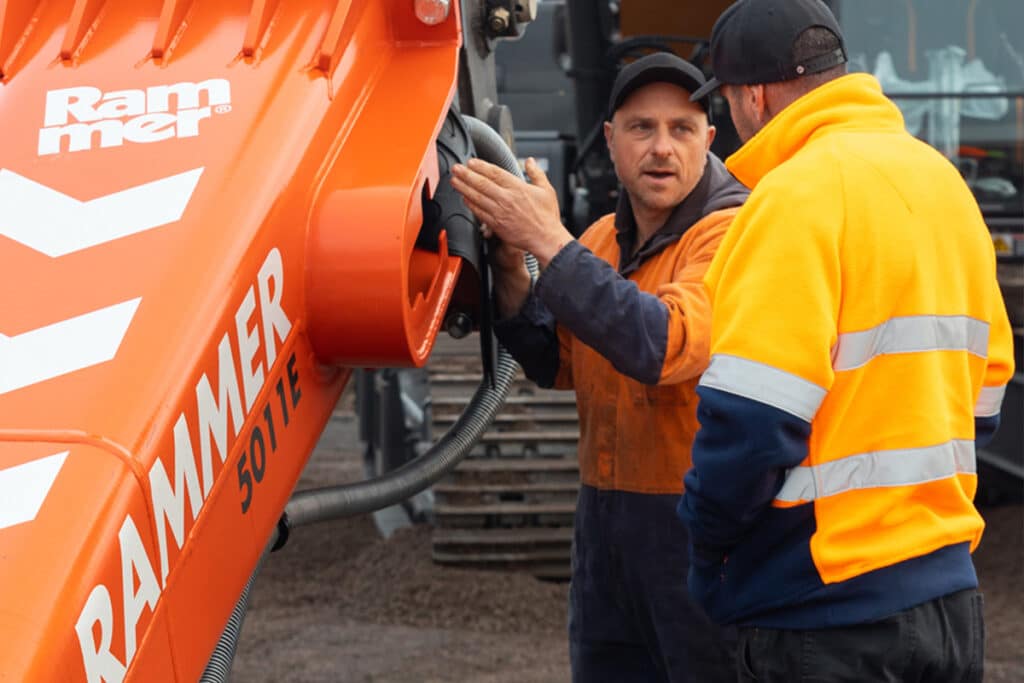
Regular Maintenance
Regular maintenance is crucial to keep rockbreaker attachments in optimal condition. Routine inspections, lubrication, and timely replacement of worn parts prevent breakdowns and extend the equipment’s lifespan. A well-maintained rockbreaker is more reliable and safer to use.
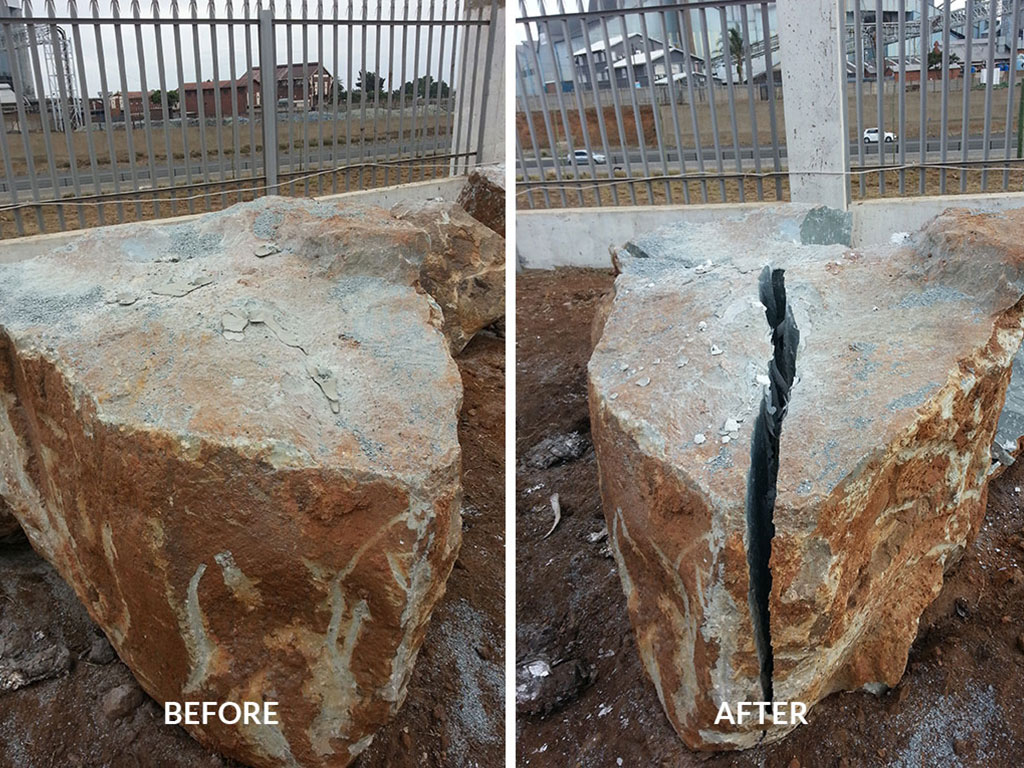
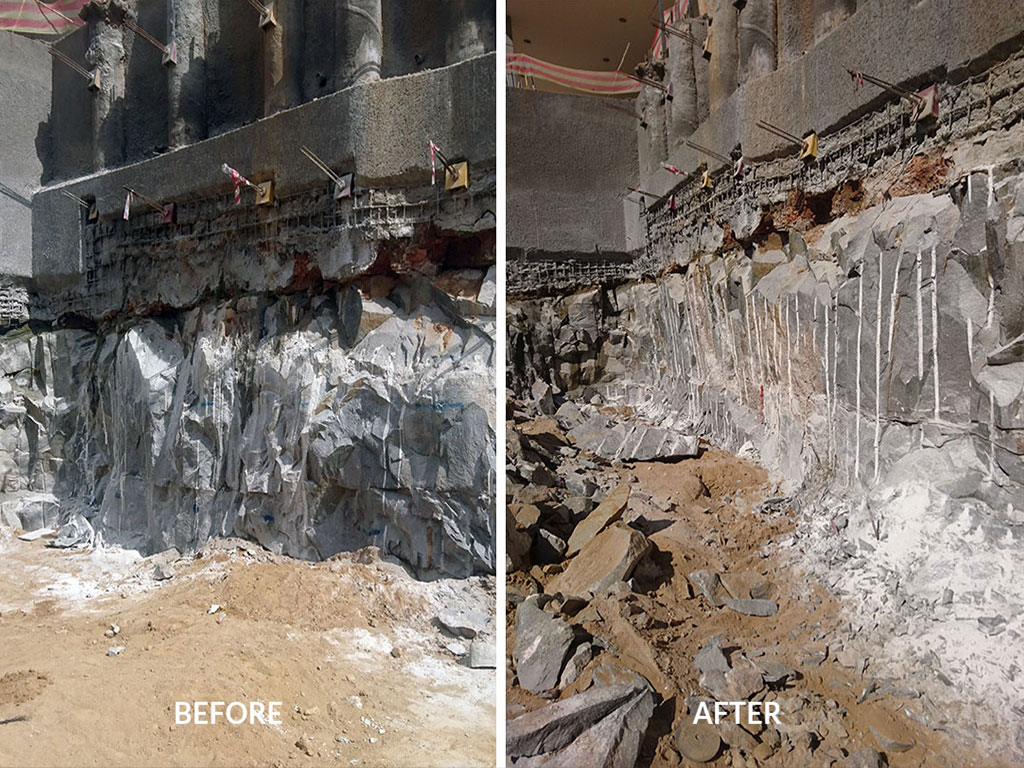
Appropriate Sizing
Selecting the right size and type of rockbreaker attachment for the job is essential. Using an undersized attachment can lead to inefficient breaking and increased wear and tear, while an oversized attachment might be cumbersome and harder to control. Properly matching the attachment to the task ensures efficiency and safety.
Adherence to Safety Protocols
Strict adherence to safety protocols cannot be overstated. Operators should always wear appropriate personal protective equipment (PPE), follow operational guidelines, and maintain awareness of their surroundings. Regular safety drills and updates to safety procedures help keep safety top of mind.
Conclusion
Rockbreaker attachments have revolutionized the mining industry by enhancing efficiency and safety. Their ability to rapidly and effectively break down large rocks, coupled with technological advancements in automation and remote control, make them indispensable tools in modern mining operations. By following best practices in training, maintenance, sizing, and safety protocols, mining companies can fully leverage the benefits of rockbreaker attachments, ensuring productive and safe operations.